In 3D printing, a diverse range of materials is now commonplace across industrial prototyping and production. While functional plastics, metals, ceramics, and even sand are widely used, ongoing research explores biomaterials and edible substances for innovative applications.
Current Landscape:
- Industrial Use: Plastics, metals like titanium and aluminium, ceramics, and sand are routinely employed in various industries for prototyping and production needs.
- Emerging Frontiers: Research initiatives are advancing 3D printing with biomaterials and food, exploring new frontiers such as tissue engineering and customizable food production.
Entry-Level Market:
- Material Limitations: At the entry-level, plastic remains dominant, typically ABS or PLA, though alternatives like Nylon are gaining traction.
- Specialized Applications: Entry-level machines are adapted for food materials like sugar and chocolate, broadening the scope of 3D printing into culinary and confectionery realms.
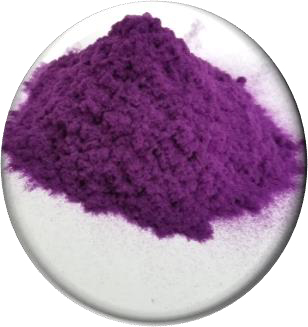
Trends and Future Directions:
- Expansion of Materials: Expect continued diversification in materials, enhancing versatility and functionality across industries.
- Accessibility: Advances in entry-level machines and materials will likely democratize 3D printing, making it more accessible for hobbyists, small businesses, and specialized applications.
1. Different StatesĀ (Powder, Filament, Pellets, Granules, Resin etc.)
2. Plastics:
Nylon (Polyamide):
Nylon is a versatile plastic used in 3D printing either as a powder for sintering processes or as a filament for Fused Deposition Modeling (FDM). It is known for its strength, flexibility, and durability, making it a reliable choice. While naturally white, Nylon can be coloured either before or after printing. It’s also used in combination with powdered aluminium to create Alumide, another common material for sintering processes.
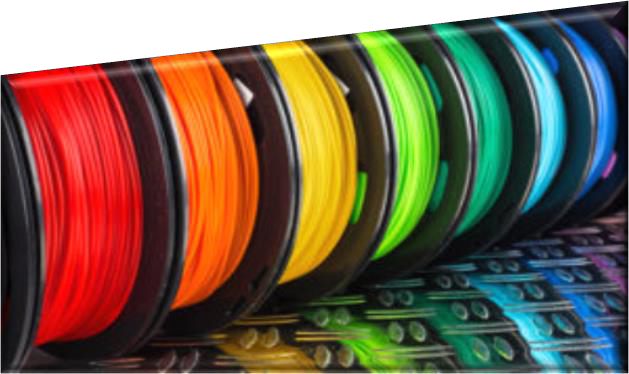
ABS (Acrylonitrile Butadiene Styrene):
ABS is another widely used plastic in 3D printing, especially on entry-level FDM printers where it’s used as filament. It is prized for its strength and comes in a wide array of colours, enhancing its popularity. ABS filament is readily available from various non-proprietary sources, contributing to its widespread use in the 3D printing community.
Key Points:
- Nylon: Offers strength, flexibility, and durability; used in both powder and filament forms for various 3D printing processes.
- ABS: Known for its strength and colour variety; commonly used in FDM printers due to accessibility and versatility.
- Applications: Both materials are integral to creating functional prototypes, durable parts, and intricate designs across different industries.
PLA (Polylactic Acid):
PLA is a bio-degradable plastic widely embraced in 3D printing for its environmental benefits. It’s used in both resin format for processes like DLP/SL and filament form for Fused Deposition Modeling (FDM). Available in a range of colours, including transparent, PLA offers versatility for various applications. However, it’s not as durable or flexible as ABS, which limits its use in certain demanding scenarios.
Lay Wood (Wood/Polymer Composite – WPC):
Lay Wood is a specialized filament designed for entry-level extrusion 3D printers. It’s a composite material blending wood fibres with polymers, replicating the appearance and texture of wood in printed objects. This unique material expands creative possibilities by allowing users to produce items with a wood-like finish directly from their printers.
Key Points:
- PLA: Known for biodegradability and versatility in colour options, suitable for both resin-based and filament-based 3D printing processes.
- Lay Wood: Offers the aesthetic appeal of wood in a printable form, enhancing the visual and tactile qualities of printed objects.
Applications:
- PLA finds use in environmentally conscious projects and applications where biodegradability is valued.
- Lay Wood is ideal for creating decorative items, prototypes, and artistic pieces that benefit from a wood-like appearance and feel.
3. Metals
- Aluminum and Cobalt Derivatives:
Industrial-grade 3D printing increasingly utilizes metals like aluminium and cobalt derivatives for their strength and versatility in various applications.
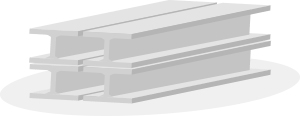
- Stainless Steel:
Stainless Steel is one of the most robust metals used in 3D printing, primarily in powder form for processes such as sintering, melting, or Electron Beam Melting (EBM). It naturally has a silver appearance but can be plated with other materials to achieve finishes like gold or bronze.
- Gold and Silver:
Recent advancements have enabled direct 3D printing of Gold and Silver, opening up significant opportunities in the jewellery sector. These metals, processed in powder form, offer both strength and aesthetic appeal.
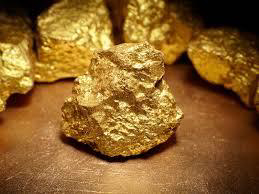
- Titanium:
Titanium remains a staple in industrial 3D printing due to its exceptional strength and durability. Supplied in powder form, it is utilized in sintering, melting, and EBM processes for a variety of industrial applications.
Key Points:
- Material Range: From aluminium to precious metals like Gold and Silver, the range of metals used in 3D printing continues to expand, catering to diverse industrial needs.
- Applications: Metals like Stainless Steel and Titanium are favoured for their strength, making them ideal for aerospace, medical, and automotive applications.
- Innovation in Jewelry: Gold and Silver’s inclusion in 3D printing enables intricate and customized designs in the jewellery industry, combining strength with aesthetic appeal
4. Ceramics
Ceramics represent a promising but relatively new frontier in 3D printing, offering diverse applications with varying levels of success. One crucial aspect to consider with ceramic materials is that, unlike some other 3D printed materials, they require traditional post-processing steps after printing.
Printing Challenges:
- Material Properties: Ceramics used in 3D printing must meet specific criteria for printing feasibility, including particle size and binder compatibility.
- Printing Process: The printing itself involves layer-by-layer deposition of ceramic material, typically in a binder or powder form.
Post-Printing Processes:
- Firing: After printing, ceramic parts must undergo firing in a kiln to achieve their final strength and durability.
- Glazing: Optionally, ceramic parts can be glazed post-firing for improved aesthetic appeal or additional functional properties.
Applications and Considerations:
- Industrial Applications: Ceramics are suitable for producing high-performance components in industries such as aerospace and healthcare.
- Artistic and Design Applications: In the creative sector, ceramic 3D printing allows for intricate and customized designs not easily achievable through traditional methods.
5. Paper
Innovative Material Choice:
Mcor Technologies employs standard A4 copier paper as the primary material for their SDL (Selective Deposition Lamination) 3D printing process. This choice distinguishes their approach from traditional 3D printing methods that often use specialized materials.
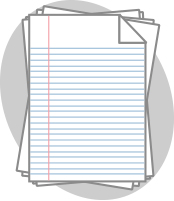
Environmental and Practical Advantages:
3D printed models using paper are safe, environmentally friendly, and easily recyclable. They require no post-processing, reducing the time and resources typically associated with finishing 3D-printed objects.
6. Bio Materials
Medical Applications:
Leading institutions are actively researching 3D printing biomaterials for medical uses. This includes pioneering efforts to print living tissues with the goal of creating human organs suitable for transplant. Researchers also aim to develop external tissues for replacing body parts, potentially transforming treatment options in healthcare.
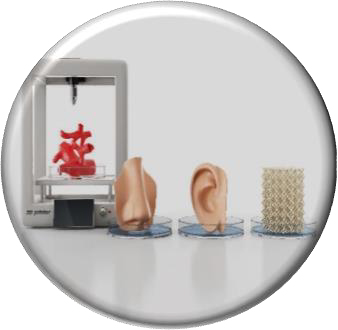
Organ Transplantation Innovations:
A significant focus of current research involves the potential to 3D print human organs. This ambitious pursuit offers hope for addressing organ shortages and improving outcomes for patients awaiting transplants, marking a potential paradigm shift in healthcare.
Food Innovation:
Beyond medical applications, researchers are exploring 3D printing for food production. Notably, there is exploration into printing meat and other foodstuffs. This research aims to revolutionize food sustainability and offer new possibilities in culinary arts and nutrition.
7. Food
Increasing Experimentation:
Recent years have seen a significant rise in experiments involving extruders for 3D printing food substances. Chocolate stands out as the most prevalent and desirable material for this technology. Additionally, there has been experimentation with printing sugar, pasta, and even meat, showcasing the diverse applications of 3D printing in the culinary field.
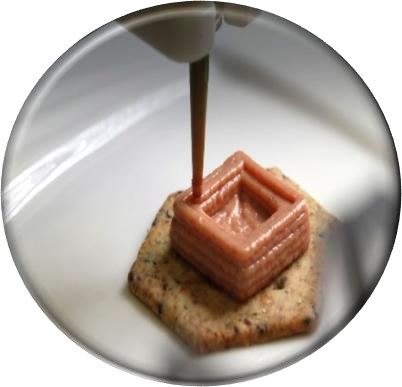
Diverse Applications:
The versatility of 3D printing extends to various food types beyond traditional ingredients. Chocolate printing exemplifies how this technology can enhance confectionery production while printing with sugar opens possibilities for intricate and decorative culinary creations. Experiments with pasta and meat highlight efforts to revolutionize food preparation methods.